CASE STUDY:
Customized Cup Holder for Vintage Automobile
Creation of a Custom-Size Cup Holder for an Automobile
DEFINING THE GOAL
A customer who owns a vintage Jaguar XJ-Series automobile wanted to retrofit the cup holder to accommodate today’s larger cups and travel mugs. He asked 3D Herndon to design and produce an insert for the existing cup holder compartment that would seamlessly integrate with the current look and feel of the interior. There were several engineering and design challenges to overcome on this project. We used a combination of 3D scanning, digital design with CAD software, and 3D printing.
The customer found that there was no existing stock part he could purchase to retrofit the cup holder that would integrate with the current look and feel of the Jaguar’s interior dash panel. The aesthetics of the cup holder were an important priority. Therefore, the challenge was to design and produce a new part that fit in the cup holder’s bay with the right look and feel. The cup holder also needed to be made from material that is able to withstand the occasionally elevated temperatures of the car’s interior, and the design needed to provide stability to prevent beverage spills from larger cups or mugs.
The Jaguar’s original cup holder was designed to hold two drinks approximately the size of a 12oz can. However, due to the space and design constraints, the new cup holder would only be able to accommodate a single larger container.
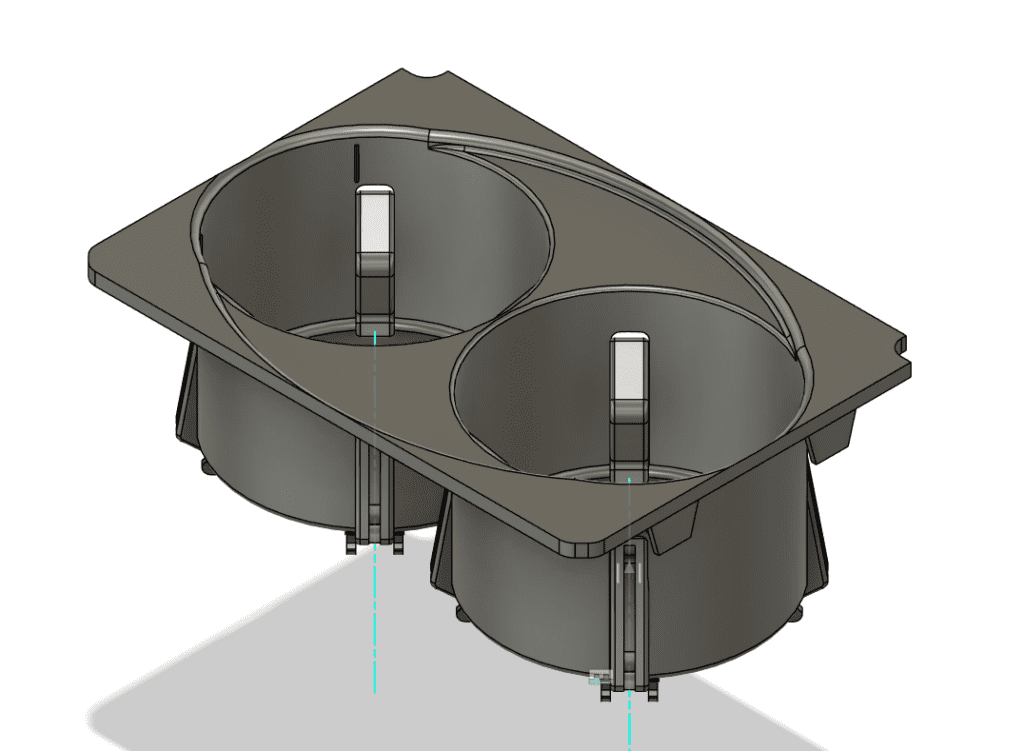
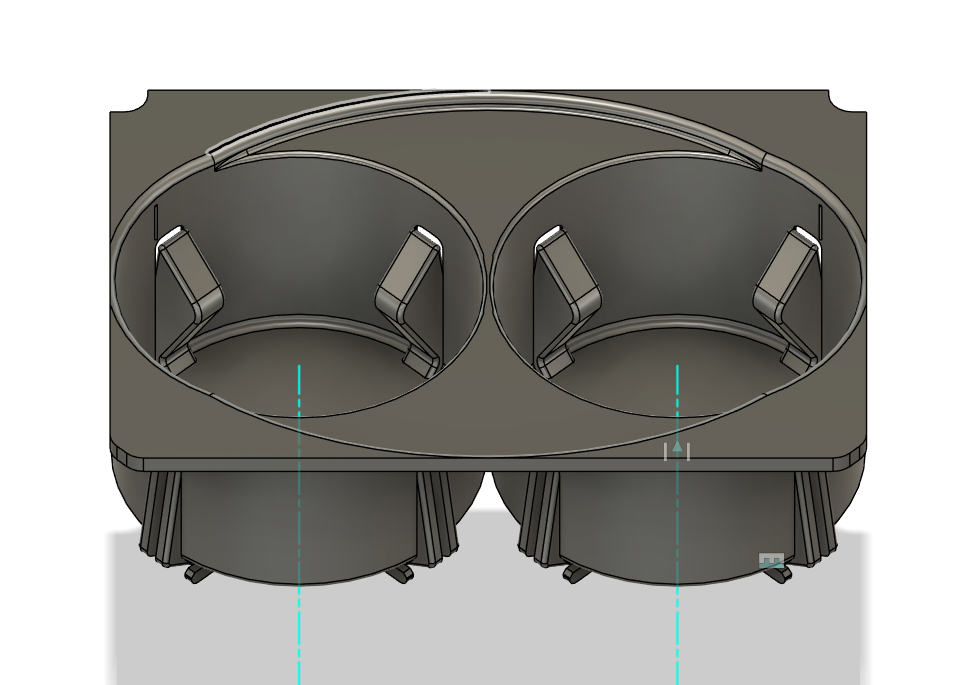
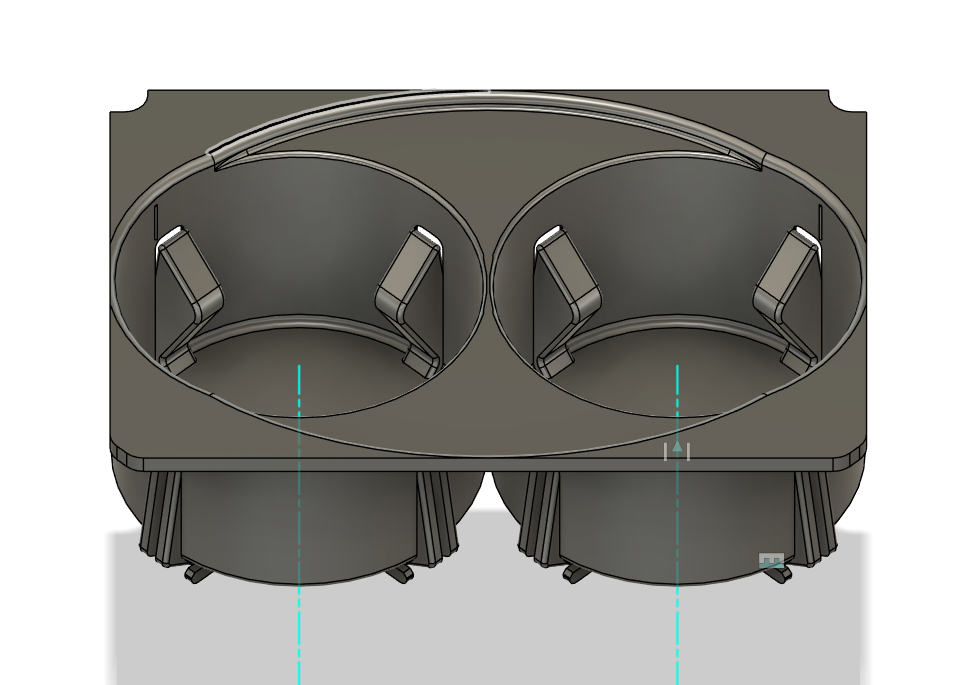
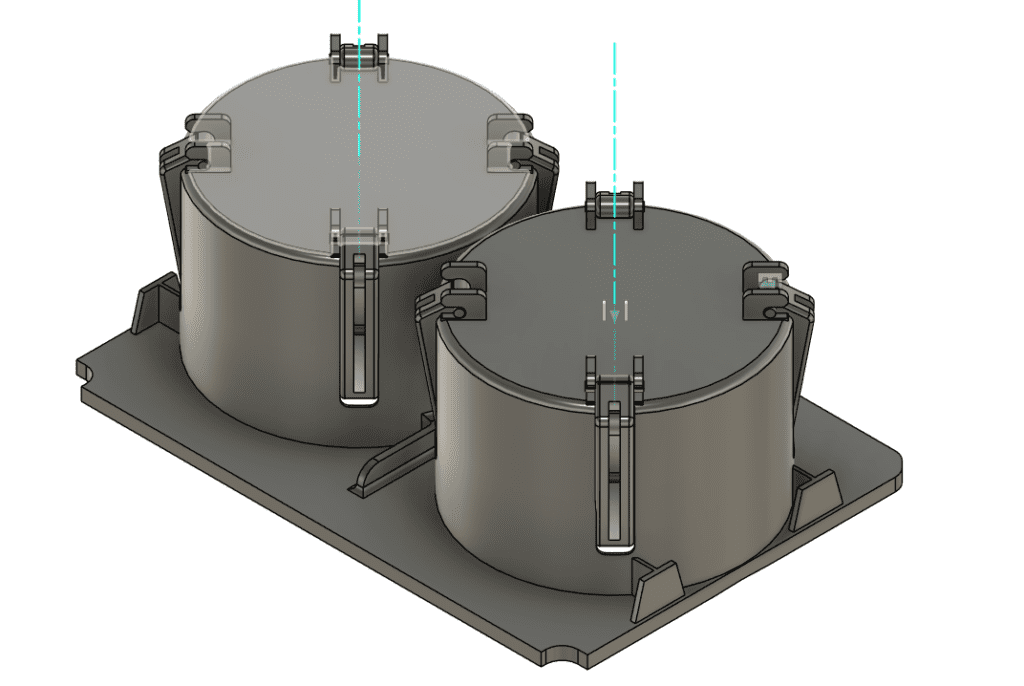
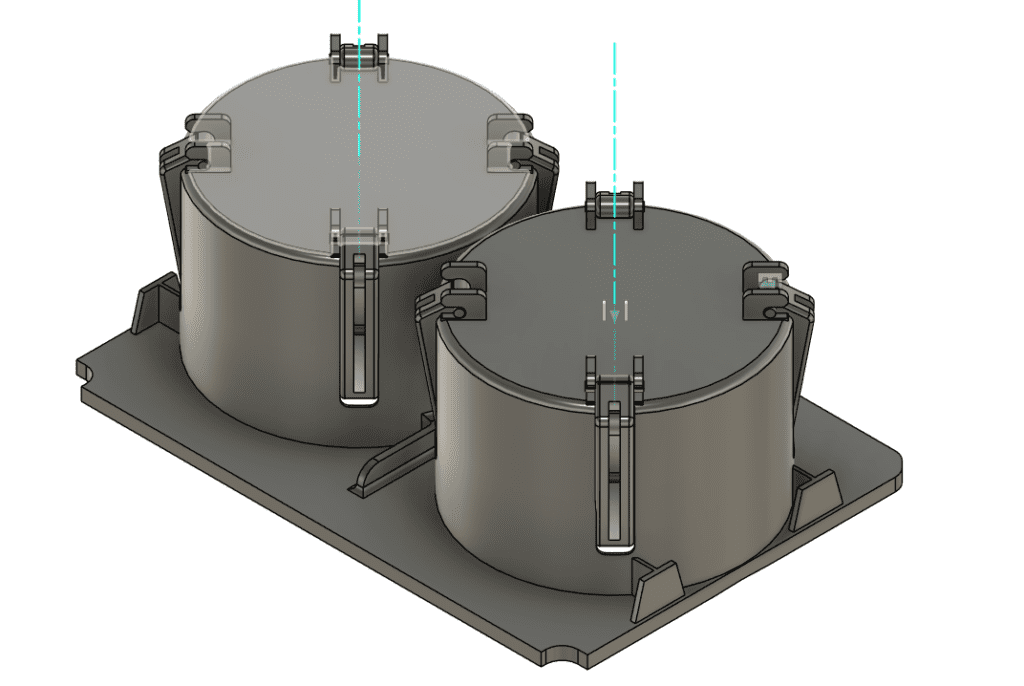
3D Herndon first used an EinScan handheld 3D scanner to capture a digital model of the Jaguar’s console including the dimensions and contours of the original cup holder. This 3D model was then used in the CAD design process with Autodesk Fusion360 software to develop the digital model of the new cup holder. The 3D model was carefully designed to seamlessly integrate the new cup holder with the car’s interior and to ensure a perfect fit within the vehicle’s console.
The new design was 3D printed using polypropylene material to provide the necessary high-temperature resistance and chemical resilience required for automotive applications. The model was then 3D printed using an UltiMaker S5 3D printer and post-processed to complete the surface finish.
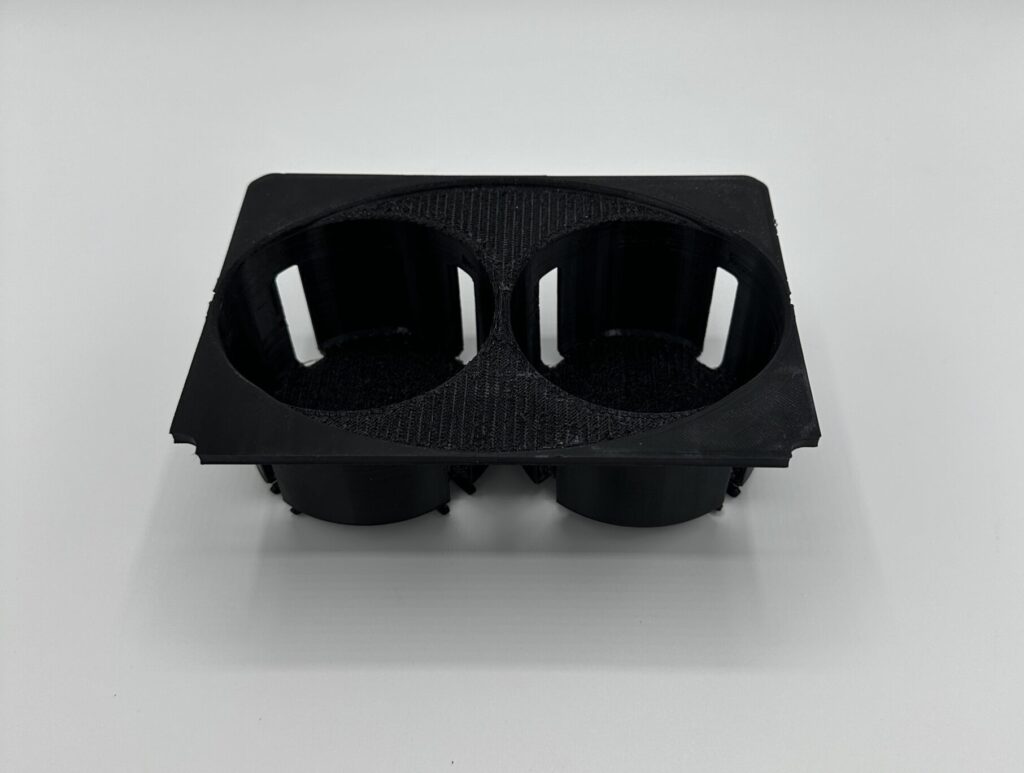
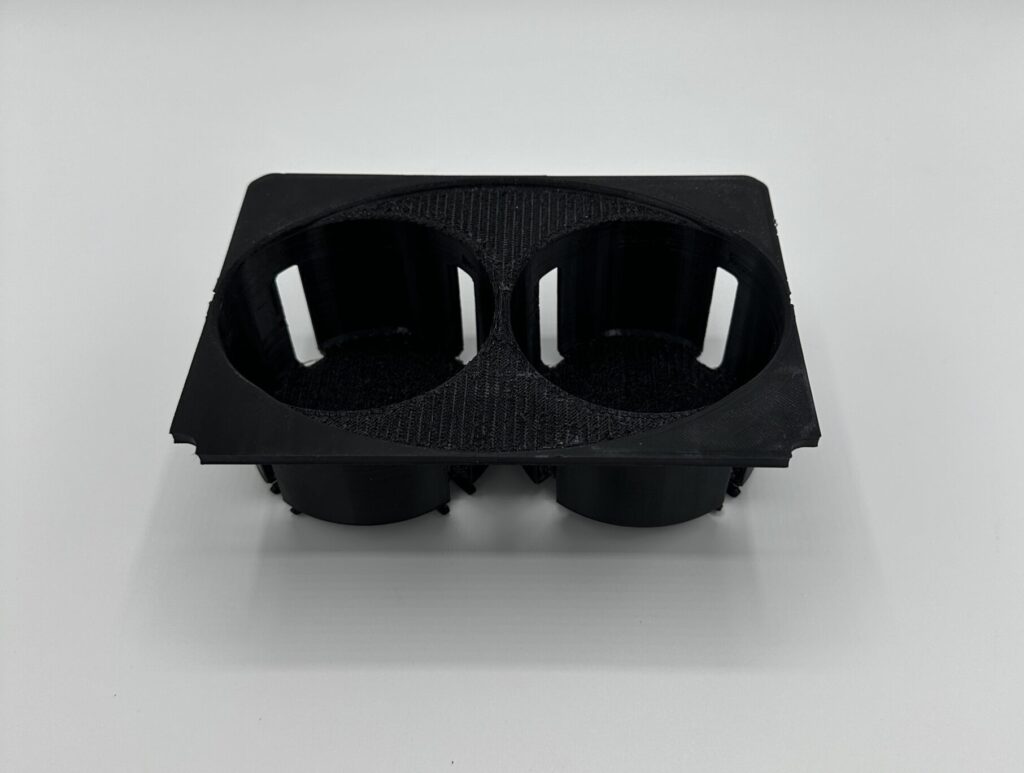
3D Herndon was able to produce a perfectly retrofitted cup holder designed to be comfortable and compatible with the modern lifestyle of the Jaguar’s driver. It was 3D printed in high-temperature and chemical-resistant polypropylene, ensuring durability and longevity. The design incorporated features to securely hold larger diameter cups and containers. This project showcased the effectiveness of combining 3D scanning, CAD design, and 3D printing to create tailored solutions for automotive applications.